Refractory Monolithics
AMANA offers the complete range of Refractory Monolithics whether it is a gunning application in an Induction Furnace or a Casting job in Holding Furnace we have the right solution. We manufacture the complete range of Castables & Mortars and have exclusive tie-ups with global manufacturing companies like Calderys for monolithic supply.


Passive Fire Bricks

High purity dense castables are refractory castables suitable for high temperature applications, all of which contain high purity refractory cement as the refractory binder. The impurity levels of all these castables are very low. These castables are available in various grades. Each grade of castables is suitable for a specific range of operational conditions. These refractory castables are hydraulic setting and can be cast or moulded to any shape and can also be suitably modified for gunning of furnace linings.
High Alumina Binders

The high alumina binders, used for making refractory castables, are calcium aluminate cements. We supply three grades of high alumina binders – Calundum, Cal-Al-70 & Cal-Al-80. Calundum, a medium purity high alumina refractory binder, sets hydraulically and when used with refractory aggregates, provides a high strength refractory castable. Cal-Al-70, a high purity refractory binder, sets hydraulically and when used along with refractory aggregates, provides a refractory castable of superior strength.
Insulation Refractory Castables

Our range of insulating castables from the Insulyte series to conserve heat in furnaces. They are light but adequately strong, and have low conductivity, thus serve as either hot face or back- up insulating refractory lining. INSULYTE castables are produced in the density range of 400 to 1600 kg/m3. They are available mainly in two different grades – medium purity and high purity. In addition to standard products, tailor-made compositions are also supplied to suit customer requirements.
Low Cement Castables

ACCMON is a series of low cement castables, having high PCE and high strength at all temperature levels. These castables are favoured in locations, where refractory abuses due to abrasion as well as application temperature are very high. These have low lime content, low porosity and high strength.
Medium Purity Dense Castables

Medium purity dense castables are suitable for use in medium temperature applications. This group of castable contain medium purity Calundum as the refractory binder. Depending on the type ofrefractory aggregates used in these castables, a series of FIRECRETE group of castable are manufactured. All these castables are used in oxidising atmospheres only. These refractory castables are hydraulic setting and can be cast or moulded to any shape, and can also be suitably modified for gunning of furnace linings.
Refractory Mortars

Refractory Mortars are joining materials for laying refractory bricks. We offer a wide range of fireclay and high alumina mortars. These mortars are used as joining materials for various insulation and high alumina bricks. Mortars like Accoset 50, Mortar 70 are suitable for different types of insulation/fire bricks. Some of the mortars are supplied as two component system, where liquid binder is separately provided with powder material. Where water is used as liquid component, the amount of water used should be such that it results in trowelling Consistency.
Refractory Plastics

Refractory Plastics are delivered in an unfired and formable condition. The mixtures consist of moistened aggregates that can be rammed into place with an air & electric hammer. These products are used both for original installations and for patching. Plastic refractories can be used in many varied applications and locations because they are essentially formed by the installer to fit the specific use area.
Conventional Castable

AMANA is a leading manufacturer of conventional castables. Our conventional castables are made with approved raw materials and include a high amount of cement. Known for their low maintenance and abrasion resistant qualities, conventional castables are used in a variety of industries including iron and steel plants, petrochemical, mineral processing, and hydrocarbon processing.
Ultra Low Cement Castable

No Cement Castable

Self Flow Castable

Erosion Resistant Castable

Phosphate Bonded Castable

Ramming Mass

Patching Refractory

Refractory patching material for blast furnace is usually used for crevice between blast furnace shell and cooling stave.and adopt the method of anhydrous impressing mortar. According to different parts and demands of blast furnaces, the refractory pressing materials of various materials such as carbon,aluminious carbon,high aluminum or clay can be selected for construction.After filling the gap between the blast furnace shell and the cooling wall,After solidification, a compact whole can be formed and can be constructed during the blast furnace downwind period.It will not affect the normal operation of blast furnace.
Gunniting Refractory

Bubble alumina refractory castable

ZIRCAR Ceramics’ Bubble Alumina is a rigid, low-density, insulating refractory comprised of hollow high-purity Alumina spheres bound in a high-purity Alumina cement. Bubble Alumina exhibits high creep resistance to temperatures as high as 1825°C (3317°F).
Vermiculite based insulation refractory castable

Vermiculite, a hydrated Mg/Al/Fe silicate mica-like clay mineral with a laminate structure. Vermiculite is a very versatile material. It has a remarkable ability to expand to many times its original volume (exfoliation) when heated (>300°C). The majority of applications call for vermiculite in its exfoliated form, and it has a wide range of applications that take advantage of its significant properties such as low bulk density, low thermal conductivity, odor-free, chemical inertness, easy handle and fire resistance. These properties make vermiculite a promising material for use as high-temperature insulating refractory material in the metallurgical industry. The service (working) temperature of vermiculite-based refractories is about 1100-1150 °C. In order to increase the working temperature and to produce a wide range of vermiculite-based refractory products, refractory binders and fillers (e.g. alumina cement, fire clays etc.) are added to the lightweight vermiculite. In this paper, the application of vermiculite as a high temperature insulating refractory material was mentioned.
Refractory Dry Out

Our Vendors and Trusted Associates
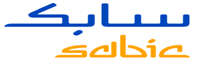
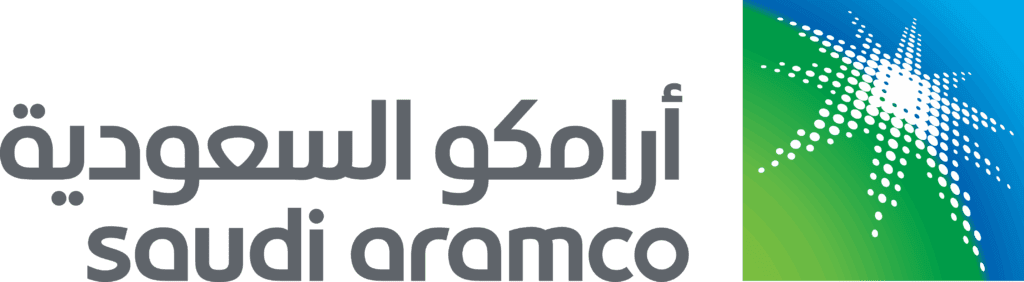
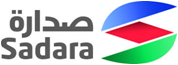
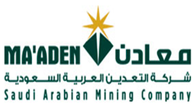
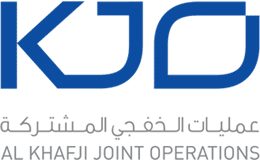
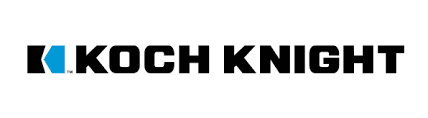
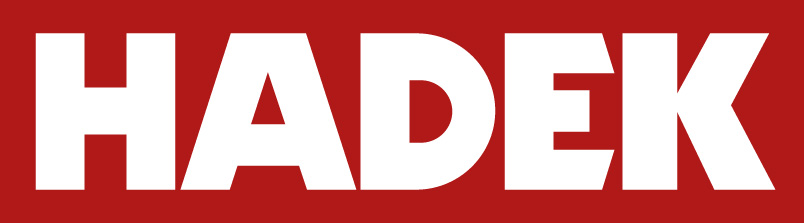
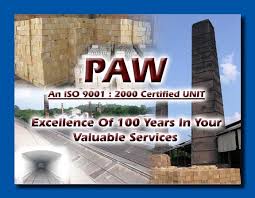
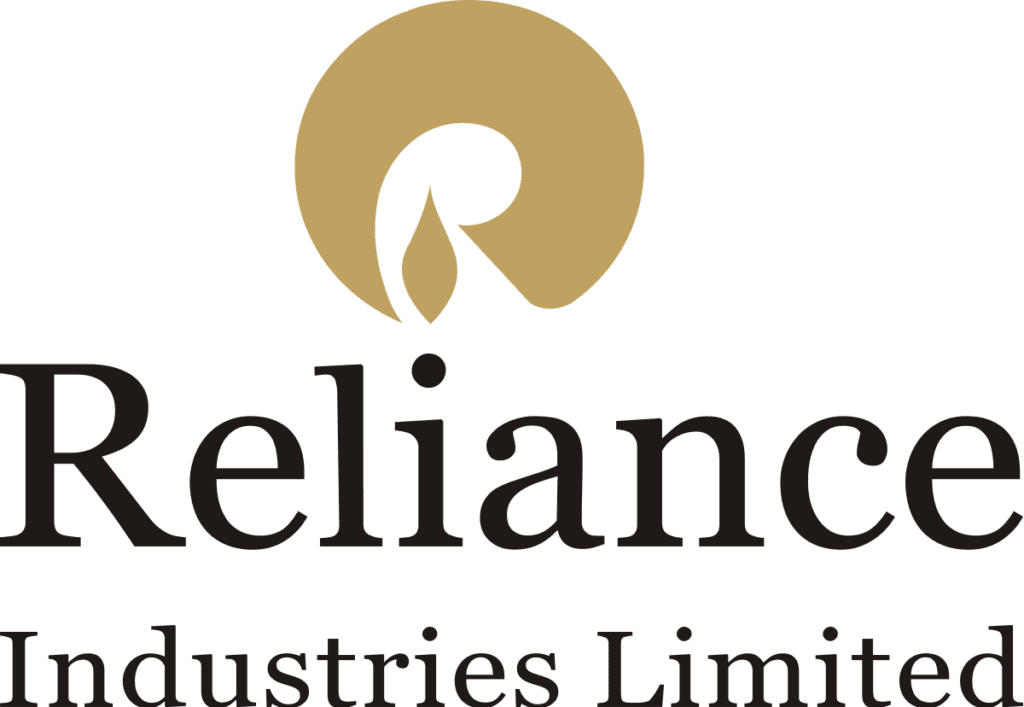
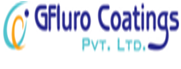
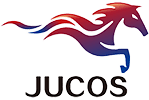
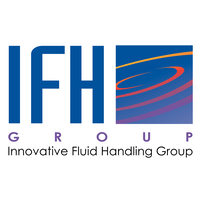
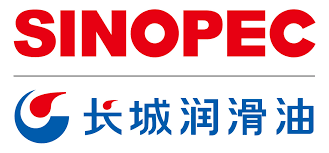
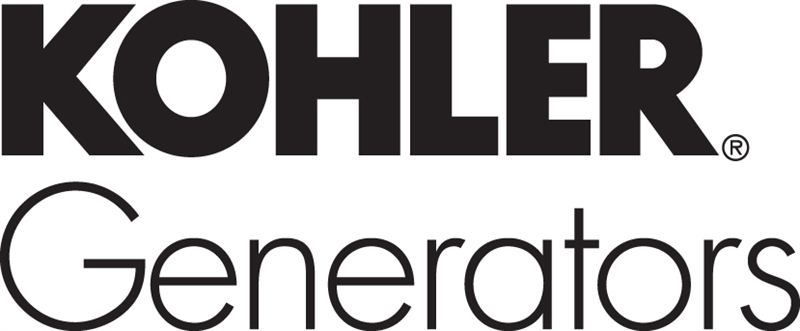
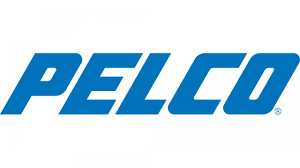
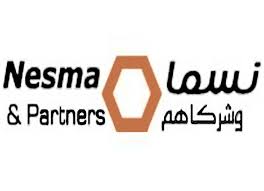
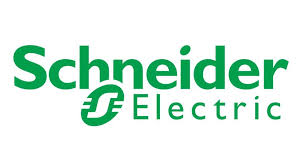
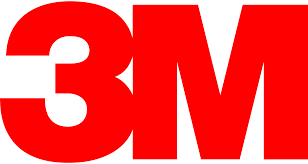
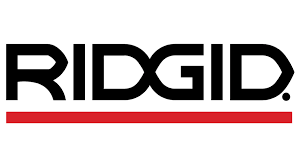
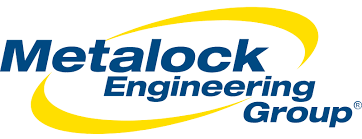
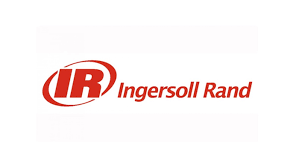
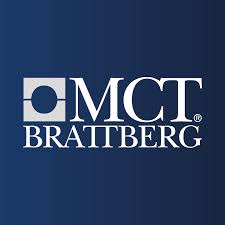
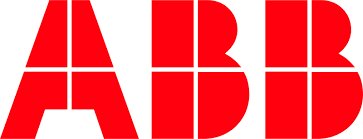